The intersection between operational technology and information technology is becoming increasingly crucial. This blog delves into the cutting-edge developments that are transforming how industries monitor, control, and optimize their operations. Through precise automation and data-driven insights, these technological advances are pioneering unprecedented levels of efficiency and productivity. Join us as we explore how these innovations are not just redefining industries, but also reshaping the future of manufacturing and production processes.
CONTENTS
Cost Reduction Strategies
One of the most impactful benefits of integrating process observation technology into industrial IT processes is the significant cost savings it can facilitate. Advanced analytics and automation systems reduce the need for manual monitoring, cutting down labor costs and minimizing human error. The team behind LJ Star Inc. says that safe, innovative, and high-quality products can be developed with reliable and cost-effective monitoring capabilities. Furthermore, insights from real-time data collection enable businesses to detect inefficiencies and identify areas for process optimization. This leads to more efficient use of resources, reducing waste and ultimately lowering operational costs.
Data Acquisition and Analysis
The backbone of any modern process observation technology lies in the ability to accurately acquire and analyze data. Sophisticated sensors measure a range of variables from pressure and temperature to flow rates in real time, ensuring that the system has a comprehensive understanding of the operational environment. The integration of Internet of Things (IoT) devices further bolsters this data acquisition by enabling a seamless flow of information across various components of the production system.
Advanced analytics software then takes over, sifting through this data to unearth patterns, predict potential issues, and advise on proactive measures. This not only streamlines the decision-making process but also lays the groundwork for predictive maintenance, highlighting possible breakdowns before they occur, thereby avoiding costly downtime and extending the lifespan of equipment.
Predictive Maintenance
Predictive maintenance stands at the forefront of maximizing industrial IT efficiency, a game-changer in minimizing maintenance costs and preventing unplanned outages. By leveraging data analytics and machine learning algorithms, process observation technology anticipates when maintenance should occur, based on actual equipment conditions rather than predetermined schedules. This approach ensures that parts are only replaced as needed, reducing both the risk of failure and the frequency of maintenance-related interruptions. It also allows companies to schedule maintenance during low-demand periods, mitigating disruption to production and maximizing uptime—a key competitive advantage in the demanding world of industrial manufacturing.
Automation Integration
In the realm of industrial IT, the synergy between process observation technology and automation is a formidable force. The heightened integration of these systems further refines the production process, allowing for a harmonious and seamless operation. Automation serves as the execution arm of data-driven decisions, implementing precise actions without delay or human intervention.
By connecting with sophisticated control systems, such as SCADA and PLCs, automation can adapt production workflows in real time, responding to the insights provided by analytics software. This level of integration results in a dynamic production environment that can self-optimize, ensuring consistent quality and peak performance at all times. Through automation integration, industries are not only achieving higher standards of productivity and reliability but also creating a safer work environment by reducing the need for direct human interaction with potentially hazardous machinery.
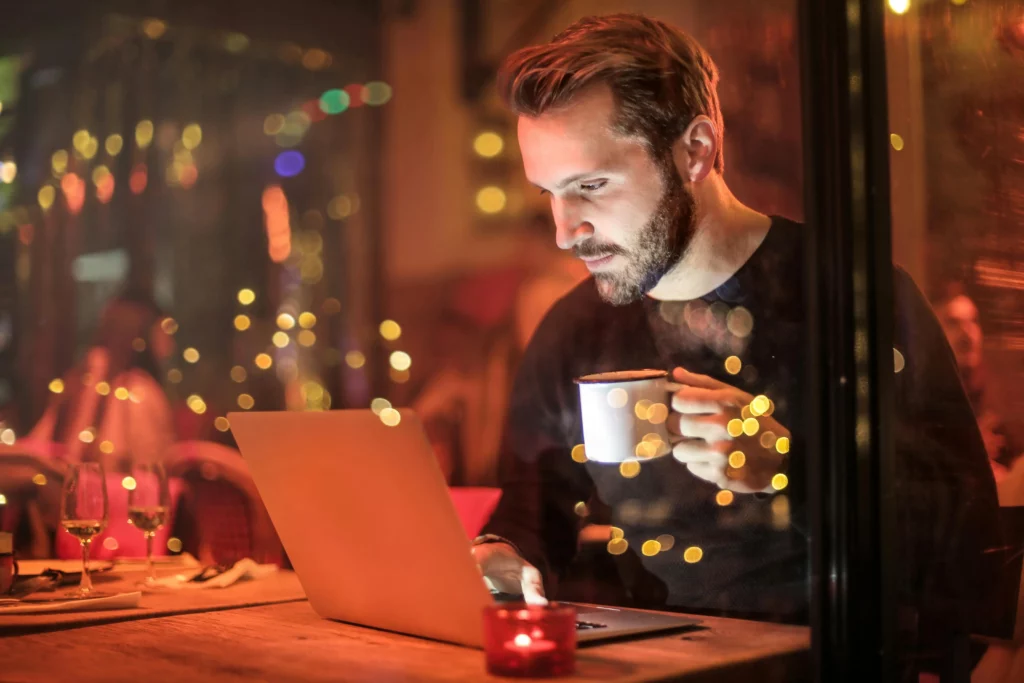
Remote Access and Control
The advent of remote access and control mechanisms within process observation technology marks a pivotal step in operational management. This facilitates a decentralized approach, allowing managers and technicians to monitor and adjust industrial processes from virtually anywhere in the world. The introduction of cloud computing and mobile interfaces has mobilized the workforce, providing the ability to respond to alerts, oversee production, and make informed decisions on the go.
Not only does this elevate the agility of operational responses, but it also improves work-life balance for the staff, who no longer need to be physically present to ensure continuous system oversight. With robust cybersecurity measures in place, remote access is becoming a staple in modern industrial settings, keeping businesses agile and resilient in the face of evolving demands and potential disruptions.
In conclusion, process observation technology is revolutionizing industrial IT processes, ushering in a new era of efficiency, cost savings, and agility. As these innovations continue to evolve and integrate, the potential for optimization and productivity in industrial settings will only grow. From predictive maintenance to remote access, there are endless possibilities for how these technologies can be leveraged to drive success in the industry. The future of industrial IT is indeed an exciting one, and we can’t wait to see where these cutting-edge developments take us next. So stay tuned for more updates on the latest process observation technology innovations.
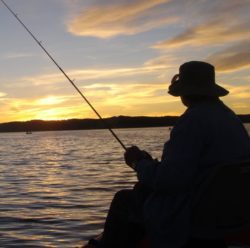
Hey, I’m David. I’ve been working as a wireless network engineer and a network administrator for 15 years. During my studies, I also worked as an ISP field technician – that’s when I met Jeremy.
I hold a bachelor’s degree in network engineering and a master’s degree in computer science and engineering. I’m also a Cisco-certified service provider.
In my professional career, I worked for router/modem manufacturers and internet providers. I like to think that I’m good at explaining network-related issues in simple terms. That’s exactly what I’m doing on this website – I’m making simple and easy-to-follow guides on how to install, set up, and troubleshoot your networking hardware. I also review new network equipment – modems, gateways, switches, routers, extenders, mesh systems, cables, etc.
My goal is to help regular users with their everyday network issues, educate them, and make them less scared of their equipment. In my articles, you can find tips on what to look for when buying new networking hardware, and how to adjust your network settings to get the most out of your wi-fi.
Since my work is closely related to computers, servers, and other network equipment, I like to spend most of my spare time outdoors. When I want to blow off some steam, I like to ride my bike. I also love hiking and swimming. When I need to calm down and clear my mind, my go-to activity is fishing.